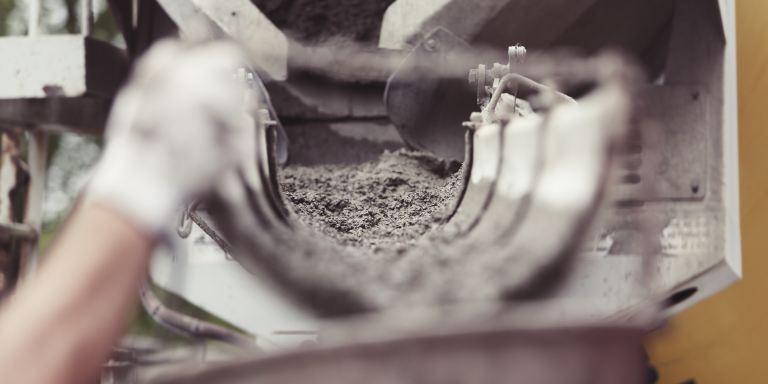
In 2018, Meta committed to minimizing its environmental footprint and is targeting net zero emissions for its value chain in 2030. However, it has plans to build eight data centers. To reduce the carbon emissions this one will generate, META’s team, with the help of Lav Varshney and Nishant Garg from the University of Urbana-Champaign, designed a low-carbon concrete using generative machine learning algorithms that they tested at the Delkab, Illinois, facility.
Concrete has been used for thousands of years to construct buildings and structures. Although it has evolved, cement is now one of its ingredients, but it is also the major source of its greenhouse gas emissions.
Concrete is the most widely used construction material in the world because of its low cost and ease of manufacture, and nearly 10 billion tons are produced each year.
It is made by mixing cement, sand and gravel with water. Cement is made by heating a mixture of clay and limestone to over 1,400°C in a kiln, which produces 600 kilograms of carbon dioxide for every ton of cement produced.
It is estimated that cement production is responsible for 8% of global carbon emissions. Research is being carried out to reduce this impact, either to replace the fossil fuels used to produce cement (hydrogen…), or to reduce its quantity in the composition of concrete, by replacing it with fly ash or slag (leftovers from iron or steel production).
Meta has fully met its 2018 commitments: to have lowered its greenhouse gas emissions in 2020 by 75% compared to 2017 and to use 100% renewable energy in the same time frame. It even exceeded these targets and achieved GHG Protocol (Greenhouse Gas Protocol) Scopes 1 and 2. To achieve Scope 3, building its data centers with the most environmentally friendly materials possible is necessary.
Meta’s low-carbon concrete built with AI
Meta’s team asked itself the following question:
“Is it possible to formulate concrete mixes with standard ingredients so that they contain half the amount of incorporated carbon as traditional formulations, but are just as strong?”
Answering this question is complex given the number of possible combinations of various concrete ingredients.
Amruta Sudhalkar, Meta Sustainability Program Manager at Meta, further stated:
“Manually optimizing a concrete formula for both sustainable and technically sound results…is a formidable challenge. The factors that go into making good concrete, especially one that tries to replace its cement content, mean not only accounting for ingredient ratios, but also external factors such as weather and location.”
Machine learning is the solution to these kinds of problems. So the Meta team partnered with рrоfеѕѕеur Lаv Vаrѕhnеy, of the deраrtеmеnt dе génіе élесtrіquе еt іnfоrmаtіquе, еt with рrоfеѕѕеur Nіѕhаnt Gаrg, from the déраrtеmеnt dе genіе сіvіl dе unіvеrѕіté dе Urbаnа-Сhаmраіgn, to train an algorithm through a еnѕеmblе dе dоnnéеѕ ѕur lа reѕіѕtаnсе to the lа соmрrеѕѕіоn of the bétоn.
1,030 concrete mixes were listed, the algorithm compared them taking into account the criteria of curing time and carbon footprint. Five mixes were selected by Meta, tested in the lab and then adjusted by concrete manufacturer Ozinga Bros.
Ozinga Bros. then tested a concrete in which 50 percent of the cement was replaced by fly ash and slag under real-world conditions for a small portion of the Elkab Center’s foundation. According to Meta, carbon emissions were found to be 40% lower than regional benchmarks and the concrete stronger in seven- and 28-day strength tests.
This test took place when temperatures were low, so the concrete took a long time to set and harden, which causes delays during construction. Meta stated:
“We strive to improve the initial strength performance of the concrete after three to five days and to account for the impact that varying environmental conditions, such as temperature and wind, can have on concrete performance.”
Translated from Grâce à l’intelligence artificielle, Meta peut construire ses centres de données avec un béton bas carbone