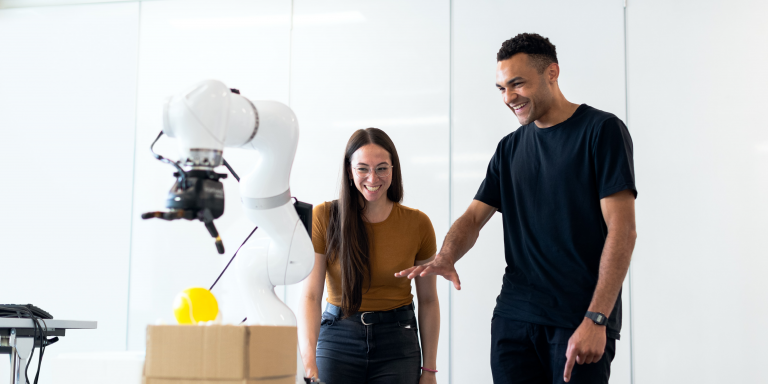
UBC Okanagan (UBCO) is located in Kelowna, British Columbia, Canada. Researchers at the Advanced Control and Intelligent Systems Laboratory are working to develop systems that allow humans and robots to interact safely and effectively. It has just developed a system to improve these interactions.
Industrial robots are programmed to optimize production by taking over manufacturing operations, welding, painting, assembly, material handling, whereas social robots do not strive to replace humans. Instead, they are designed to assist humans in service industries, typically mobile, lightweight and programmed to operate in a variety of environments. Human-robot collaboration (HRC), or cobotics, is a branch of robotics that redefines the robot’s place as working “with” and not “instead of” the operator. Humans will increasingly be required to work with robots in the same space and it is imperative to make it safe. HRC research in the industry is therefore aimed at the safety of humans and robots but also at the way they collaborate and, in addition, it measures the level of autonomy and adaptability of robots to train them for various tasks.
The UBCO School of Engineering, following the SAE guidelines for autonomous vehicles, has developed a system to improve interactions between people and robots and has recently published this study. It is titled: “An Investigation of Robot Learning Strategies for Human-Robot Collaboration in Industrial Settings.”
Debasita Mukherjee, PhD student and lead author of the study said:
“How people safely interact with robots is at the forefront of current research related to automation and manufacturing.”
She continued:
“It is extremely important that manufacturing robots perform their tasks in the safest and most efficient way possible.In order to make these automated machines as intelligent as possible, we are developing systems that perceive their environment and perform tasks in the same way as their human partners.”
For successful RHC in an industrial setting, robots must be intelligent and mobile, but also have awareness of their environment and the human collaborator. For Debasita Mukherjee, “adaptingto uncertainty in an industrial environment is the biggest obstacle.” In the research, she introduces some rules for human-robot interactions in an industrial setting and tests their effectiveness. She explains:
“Increasing levels of automation are standardized and accepted by the automotive industry, but other industrial environments, while relatively static, do not have the same standards. In the future, not only will industrial automated systems continue to use sensors to enable perception and communication similar to human capabilities, but they will also adapt and communicate in real time with their environment. “
To develop these systems, the study authors used artificial intelligence and machine learning to guide the machines. They present the different machine learning (ML) methodologies and their industrial applications for adaptive collaborative robots.
The goal of the research is “to achieve the seamless team dynamics and communication fluidity of a fully human team while using robots.”
Sources: https: //doi.org/10.1016/j.rcim.2021.102231
Translated from Des chercheurs de l’UBCO, en Colombie-Britannique, ont mis au point un système pour améliorer les interactions homme-robot